Gravure printing is one of the most versatile and efficient methods for high-quality printing, particularly in industries requiring large-volume production of printed materials. This process uses a rotary printing press that utilizes engraved cylinders to transfer ink onto the substrate, making it suitable for a wide range of applications, from packaging materials to magazines and even wallpaper. The gravure printing machine’s ability to produce consistent, high-quality images at high speeds makes it a preferred choice in many commercial printing industries.
The core of the gravure printing process lies in the engraved cylinder. These cylinders are etched with the image or pattern to be printed, with different depths and patterns for varying levels of ink transfer. The ink, which is typically liquid and of a very high viscosity, is applied to the engraved cylinder. Excess ink is removed by a doctor blade, leaving ink only in the engraved cells of the cylinder. As the substrate, often made of paper, plastic film, or foil, passes under the cylinder, the ink is transferred, creating a high-resolution print.
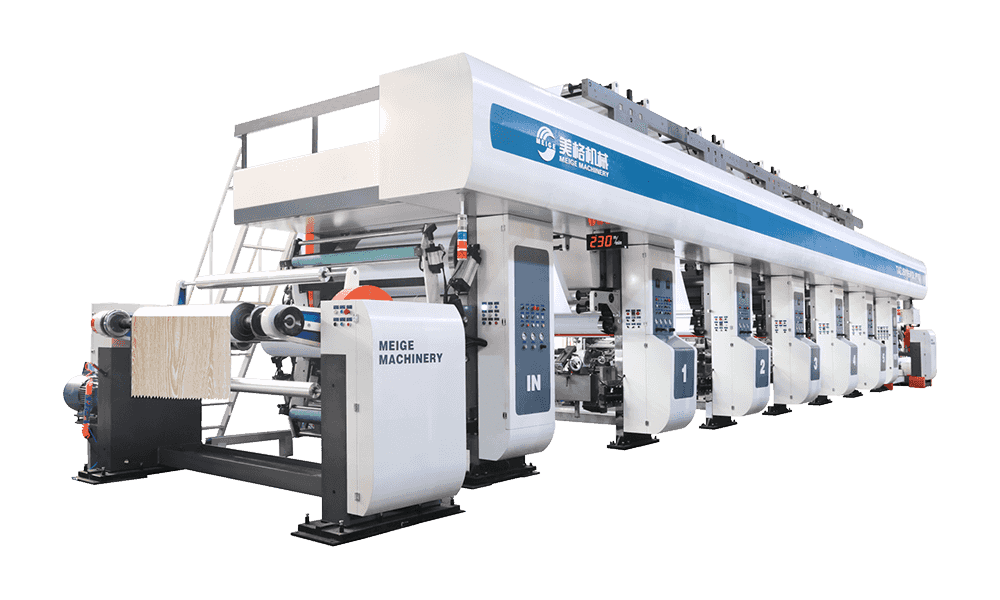
One of the major benefits of gravure printing is its ability to print with a wide range of ink types and substrates. Unlike some printing methods that are limited by substrate compatibility, gravure can work with virtually any surface, from thin films to thicker materials. This flexibility makes it ideal for packaging, especially for products that require intricate designs or complex graphics, such as food packaging, cosmetics, and electronics.
Another key advantage of gravure printing machines is their speed. Once the machine is set up, gravure presses can operate at speeds that surpass those of many other printing technologies, such as flexographic or offset printing. This high-speed capability, coupled with its high image quality, makes gravure the go-to choice for long-run printing jobs. The initial setup costs of gravure presses can be high, particularly due to the engraving process for the cylinders, but the cost per unit decreases significantly in long production runs, making it cost-effective for high-volume projects.
Gravure printing also excels in producing rich, vibrant colors with excellent color accuracy. This is especially important in markets like packaging, where visual appeal can be a deciding factor in product sales. The deep impression created by the engraved cylinders ensures that the ink adheres well to the material, leading to a more durable and long-lasting print. This durability is particularly useful for products exposed to elements such as sunlight or moisture, as the ink is less likely to fade or smudge compared to other printing methods.